Comparison with Alternative Lining Solutions
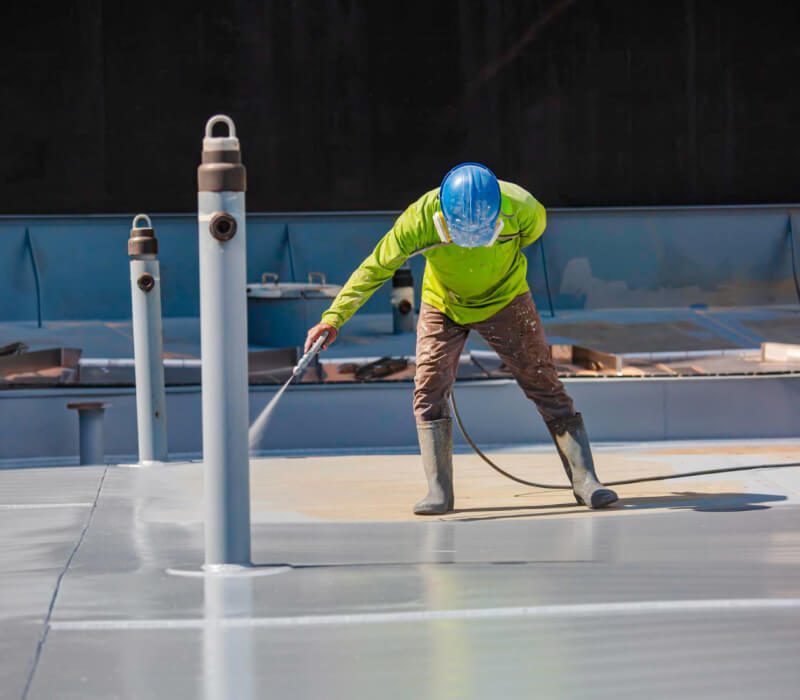
GRP Lining Vs Epoxy Lining
The material for lining that is to be used in any given industrial application should be selected with high care. GRP lining and epoxy lining are two major lining materials, differing in properties and suited for different situations.
Composition And Structure
GRP lining:
- Materials: It is made of a polymer matrix to which glass fibers are added for reinforcement.
- Structure: In GRP, the glass fibers contribute to the strength, and the resin matrix gives chemical and moisture resistance.
- Common Resins: Polyester and vinyl ester and epoxy resins are the commonest ones used in GRP lining.
Epoxy Lining:
- Materials: The lining shall be of pure epoxy resin, added to with additives or fillers to give any property that the pure epoxy lacks.
- Structure: Epoxy lining consists of a homogenous material without reinforcement. It depends wholly on the strength that the epoxy resin can provide.
- Additives: can include pigments, flame retardants, and hardeners in order to change properties.
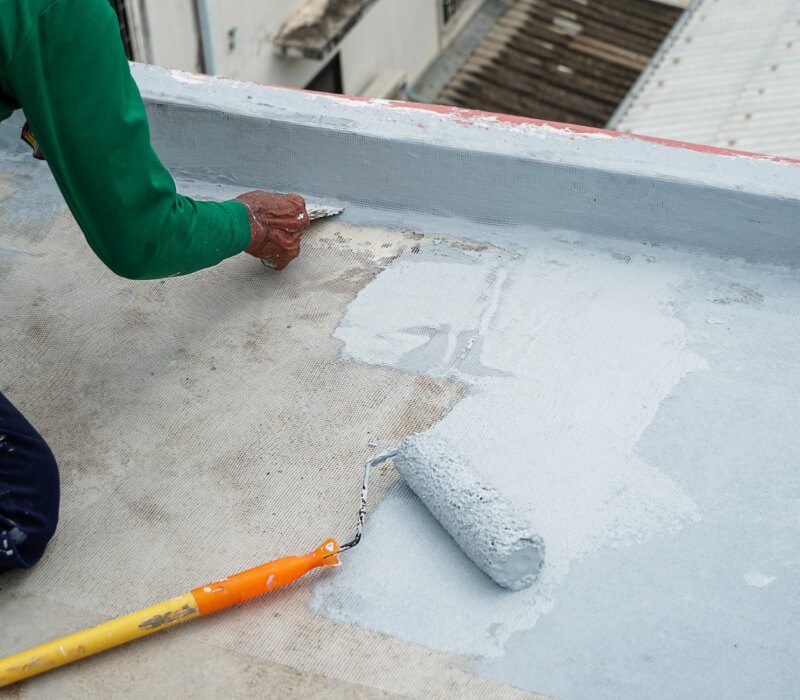
Performance Characteristics:
Property | GRP Lining | Epoxy Lining |
---|---|---|
Mechanical Strength | High tensile strength due to glass fiber reinforcement. | Moderate to high, depending on the epoxy formulation. |
Chemical Resistance | Excellent, particularly with vinyl ester or epoxy resins. | Very high, especially against acids and alkalis. |
Durability | Long-lasting, with excellent wear resistance. | Highly durable, especially in chemical environments. |
Flexibility | Moderate, with some flexibility depending on fiber orientation. | Rigid, with minimal flexibility. |
Temperature Resistance | Can withstand moderate to high temperatures. | High resistance, suitable for extreme temperatures. |
Cost | Generally lower, depending on resin type and application. | Typically higher due to the cost of pure epoxy resin. |
Application Suitability:
Application | GRP Lining | Epoxy Lining |
---|---|---|
Chemical Storage Tanks | Excellent, especially with vinyl ester resins. | Ideal, particularly in environments with strong acids or alkalis. |
Pipelines | Suitable, especially where mechanical strength is required. | Ideal for pipelines carrying aggressive chemicals. |
Flooring | Can be used, though epoxy is often preferred. | Widely used in industrial flooring due to its durability. |
Marine Applications | Highly suitable, with excellent water and corrosion resistance. | Suitable, but GRP may be preferred for its flexibility and impact resistance. |
FAQ
GRP (Glass Reinforced Plastic) lining is a composite material used to provide corrosion resistance and strength to various surfaces, typically in industrial applications.
Epoxy lining involves applying a protective coating made from epoxy resin, which provides a durable, corrosion-resistant surface for a variety of substrates.
GRP lining uses a composite material with glass fibers for enhanced strength and durability, while Epoxy lining uses a resin-based coating that cures to form a tough, protective layer.
GRP lining offers high strength-to-weight ratio, excellent corrosion resistance, and long-lasting performance in harsh environments.
Epoxy lining provides a strong, chemical-resistant coating that is ideal for protecting surfaces from corrosion, wear, and chemical damage.
Cost-effectiveness depends on the application and required performance. GRP lining may be more expensive initially but can offer longer-term benefits, while Epoxy lining may be more economical for less demanding applications.
GRP lining excels in high-stress and abrasive environments due to its strength. Epoxy lining is suitable for moderate conditions and offers superior chemical resistance.